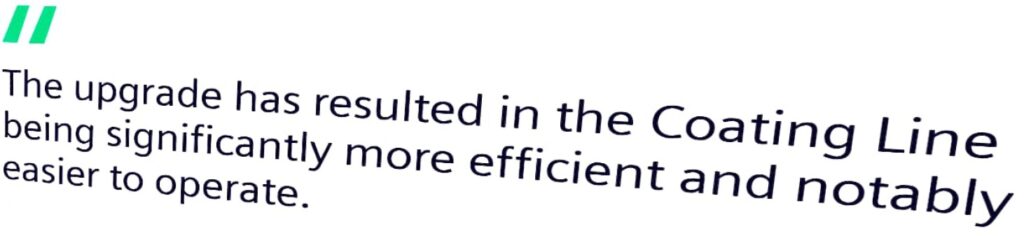
A coating machine installed in 1988 was facing increasing reliability and operational challenges due to its age. Key issues included:
- Unpredictable Start-ups: The machine suffered from erratic start-ups, impacting the consistency of production
- Frequent Recalibrations: Maintenance required regular recalibration of controls to maintain system reliability
- Obsolete Motor Components: The DC ATEX-certified motors were no longer available on the market, and existing units were becoming increasingly unserviceable.
- High Energy Losses in Transmission: High energy losses occurred due to inefficient PIV transmissions and aging gearboxes
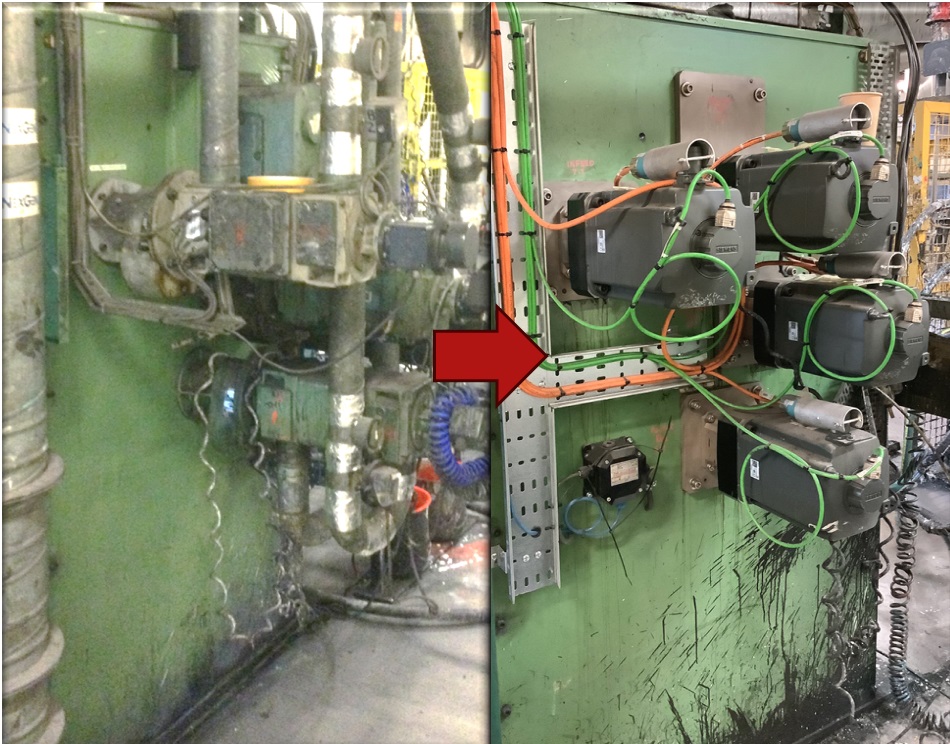
Solution:
The customer needed a comprehensive solution to address the following:
- Motor Obsolescence: Replace outdated motors to improve operational reliability and reduce unpredictable start-ups.
- Improved Product Quality: Frequent poor coating quality, wrap-ups, and web breaks needed to be minimized.
- Flexibility in Production: The upgraded system should be versatile enough to accommodate various products without requiring extensive reconfiguration.
- Full PROFISAFE Integration: The machine was eqipped with a full PROFISAFE solution that incorporated safe speed monitoring. This improved operational safety and reducing risks during maintenance and production changes.
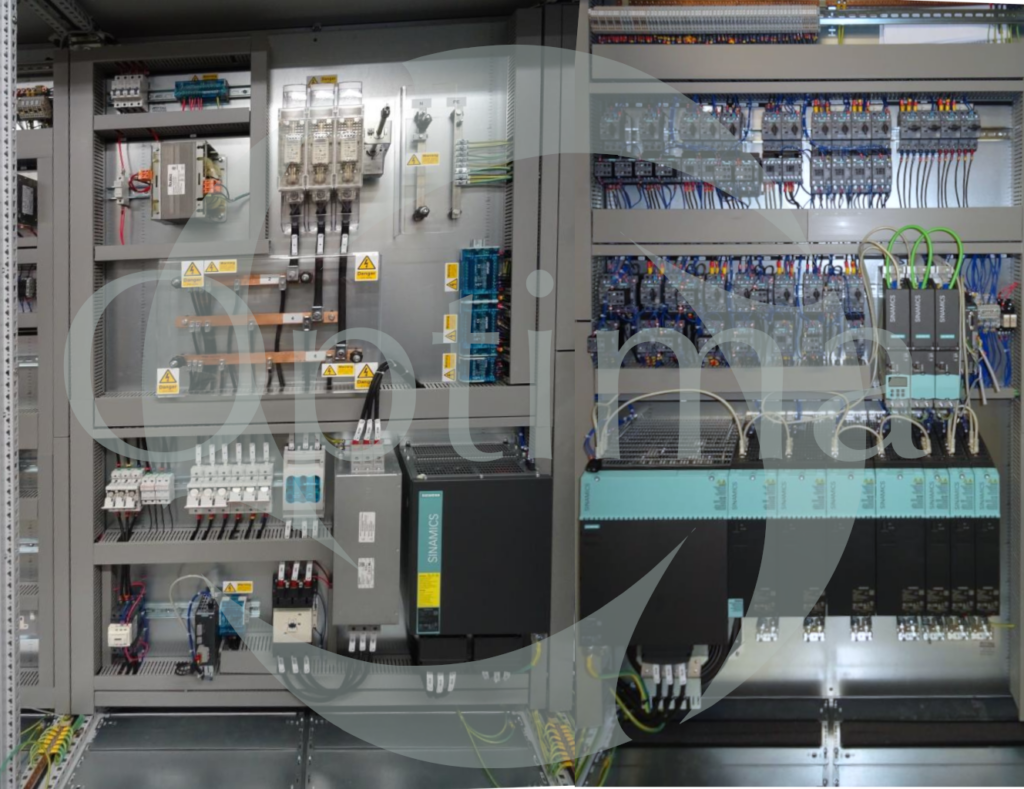
Benefits: Following the upgrade, the machine achieved several substantial improvements, making it one of the most energy-efficient unit in the factory, even outperforming newer equipment.
Key benefits included:
- Enhanced Energy Efficiency: The new servo motors and optimized drive system minimized energy waste, eliminating the need for ventilation or purging, which reduced fan energy consumption.
- Increased Production Speed: The upgraded machine operates at a higher production speed without compromising product quality, resulting in improved throughput.
- Reduced Mainternance Requirements: The new configuration eliminated the need for regular recalibration, easing the workload on maintenance staff.
- Improved Operator Satisfaction: Operators appreciated the simplified “one-touch” start functionality, which made operation straightforward and reduced the likelihood of errors.
- Minimized Product Losses: By eliminating web breaks and improving coating consistency, the machine reduced material waste and product rework.
This comprehensive machine upgrade resulted in a safer, more energy-efficient, and flexible production process, meeting the customer’s needs for reliability, flexibility, and operational efficiency. With improved equipment uptime, increased production speed, and lower energy costs, the customer has a future-proofed machine that supports long-term productivity and cost savings.
Optima are now in place to provide ongoing support and uprgades using our Remote Access system
Optima are an approved Siemens Drive Systems Integrator with a 30 year track record of delivering results on complex automation applications